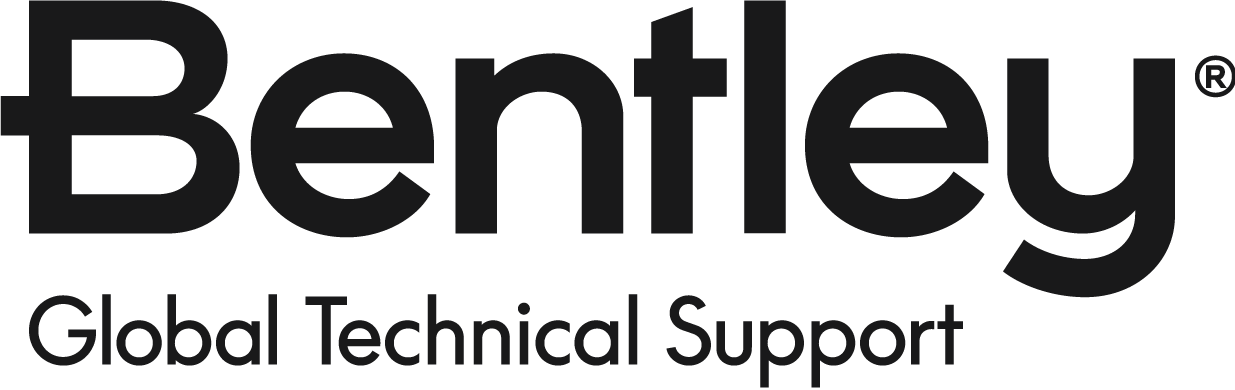
| | | |
| Applies To | | |
| | | |
| Product(s): | STAAD.Pro | |
| Version(s): | All | |
| Environment: | N/A | |
| Area: | Analysis Solutions | |
| Subarea: | Pushover Analysis | |
| Original Author: | Bentley Technical Support Group | |
| | | |
Pushover Analysis
of
Steel Structure using STAAD
By
Bentley Systems
Mr. Kalavagunta Sreedhar
Definition
Pushover Analysis option will allow engineers to perform pushover analysis as per FEMA 356 : 2000 and ATC 40. Pushover analysis is a static, nonlinear procedure using simplified nonlinear technique to estimate seismic structural deformations. It is an incremental static analysis used to determine the force-displacement relationship, or the capacity curve, for a structure or structural element.
The analysis involves applying horizontal loads, in a prescribed pattern, to the structure incrementally, i.e. pushing the structure and plotting the total applied shear force and associated lateral displacement at each increment, until the structure or collapse condition.
Purpose of Pushover Analysis
It is expected that most buildings rehabilitated in accordance with a standard, would perform within the desired levels when subjected to the design earthquakes. Structures designed according to the existing seismic codes provide minimum safety to preserve life and in a major earthquake, they assure at least gravity-load-bearing elements of non-essential facilities will still function and provide some margin of safety. However, compliance with the standard does not guarantee such performance. They typically do not address performance of non-structural components neither provide differences in performance between different structural systems. This is because it cannot accurately estimate the inelastic strength and deformation of each member due to linear elastic analysis. Although an elastic analysis gives a good indication of elastic capacity of structures and indicates where first yielding will occur, it cannot predict failure mechanisms and account for redistribution of forces during progressive yielding.
To overcome this disadvantages different nonlinear static analysis method is used to estimate the inelastic seismic performance of structures, and as the result, the structural safety can be secured against an earthquake. Inelastic analysis procedures help demonstrate how buildings really work by identifying modes of failure and the potential for progressive collapse. The use of inelastic procedures for design and evaluation helps engineers to understand how structures will behave when subjected to major earthquakes, where it is assumed that the elastic capacity of the structure will be exceeded. This resolves some of the uncertainties associated with code and elastic procedures. The overall capacity of a structure depends on the strength and deformation capacities of the individual components of the structure. In order to determine capacities beyond the elastic limit some form of nonlinear analysis, like Pushover Analysis, is required.
Theory on which it is based
There are two nonlinear procedures using pushover methods:
a) Capacity Spectrum Method,
b) Displacement Coefficient Method.
In STAAD Displacement Coefficient method has been followed.
Displacement Coefficient Method is to find target displacement which is the maximum displacement that the structure is likely to be experienced during the design earthquake. It provides a numerical process for estimating the displacement demand on the structure, by using a bilinear representation of capacity curve and a series of modification factors, or coefficients, to calculate a target displacement. Refer Section 3.3.3.3.2 of FEMA 356: 2000 for detailed description of calculation of target displacement
Types of non-linearity
Both geometric and material non-linearities are considered in this static nonlinear pushover analysis.
This is a type of non-linearity where the structure is still elastic, but the effects of large deflections cause the geometry of the structure to change, so that linear elastic theory breaks down. Typical problems that lie in this category are the elastic instability of structures, such as in the Euler bulking of struts and the large deflection analysis of a beam-column member. In general, it can be said that for geometrical non-linearity, an axially applied compressive force in a member decreases its bending stiffness, but an axially applied tensile force increases its bending stiffness. In addition, P-Delta effect is also included in this concept.
In this type of non-linearity, material undergoes plastic deformation. Material non-linearity can be modeled as discrete hinges at a number of locations along the length of a frame (beam or column) element and a discrete hinge for a brace element as discrete material fibers distributed over the cross-section of the element, or as a series of material points throughout the element.
Frame element hinge properties
Discrete hinge properties for frame elements are based on FEMA-356 criteria as per Section 5.5.2.2.2.
Figure1.6 Generalized Force-Deformation Relationship for Components
- Point A is the origin
- Point B represents yielding. No deformation occurs in the hinge up to point B, regardless of the deformation value specified for point B. The displacement (rotation or axial elongation as the case may be) will be subtracted from the displacements at points C, D and E. Only plastic deformation beyond point B will be exhibited by hinge.
- Point C represents ultimate capacity of plastic hinge. At this point hinge strength degradation begins (hinge starts shedding load) until it reaches point D.
- Point D represents the residual strength of the plastic hinge. Beyond point D the component responds with substantially strength to point E.
- Point E represnts total failure. At deformation greater than point E the plastic hinge will drop load to zero.
This diagram represent for those component actions which are ductile (e.g. Hinge formation for bending moment about local z axis of beam). For force-controlled action, Type 3 curve is followed. Refer Table C2-1 of FEMA 356 : 2000 for examples of possible deformation-controlled and force-controlled actions.
Lateral Load Distribution as per Section 3.3.3.2.3 Chapter 3 FEMA 356
Lateral load can be applied by following three methods.
Method 1
The vertical distribution of the base shear shall be as specified in this section for all buildings. The lateral load applied at any floor level x shall be determined in accordance with equation (1-8-1) and equation (1-8-2):
Fx = CvxV …………………………. (1-8-1)
where
wxhkx
Cvx = -------------------- …………………………. (1-8-2)
n
S wihki
i = 1
Method 2
A vertical distribution proportional to the shape of the fundamental mode in the direction under consideration is performed. Use of this distribution shall be permitted only when more than 75% of the total mass participates in the fundamental mode in the direction under consideration, and the uniform distribution is also used.
wx Fx
Fx = --------------- V
n
S wi Fi
i = 1
Method 3
A vertical distribution is performed consisting of lateral forces at each level proportional to the total mass at each level .
wx
Fx = --------- V
n
S wi
i = 1
where,
Cvx = Vertical distribution factor
k = 2.0 for T 2.5 seconds ≥
= 1.0 for T 0.5 seconds ≤
Linear interpolation shall be used to calculate values of for intermediate values of k for
intermediate values of T.
V = User defined base shear
wi = Portion of the total building weight W located on or assigned to floor level i
wx = Portion of the total building weight W located on or assigned to floor level x
hi = Height (in ft) from the base to floor level i
hx = Height (in ft) from the base to floor level x
Fx = Amplitude of mode a floor level x
Masses
The method involves 2 matrices – the stiffness matrix and the mass matrix.
The stiffness matrix, usually called the [K] matrix, is assembled using data such as member and element lengths, member and element properties, modules of elasticity, poison’s ratio, member and element release, member offsets, support information, etc.
For assembling the mass matrix, called the [M] matrix, the input is weights, not masses. Internally, STAAD will convert weights to masses by dividing the input by “g” the acceleration due to gravity.
Example.
Illustrate the procedure and results find the bellow STAAD example
STAAD PLANE
START JOB INFORMATION
ENGINEER DATE 07-Oct-05
END JOB INFORMATION
INPUT WIDTH 79
UNIT INCHES KIP
JOINT COORDINATES
1 0 0 0; 2 0 118.11 0; 3 118.11 118.11 0; 4 118.11 0 0; 5 0 236.22 0;
6 118.11 236.22 0; 7 0 354.331 0; 8 118.11 354.331 0; 9 0 472.441 0;
10 118.11 472.441 0; 11 236.22 118.11 0; 12 236.22 0 0; 13 236.22 236.22 0;
14 236.22 354.331 0; 15 236.22 472.441 0;
MEMBER INCIDENCES
1 1 2; 2 2 3; 3 3 4; 4 2 5; 5 5 6; 6 6 3; 7 5 7; 8 7 8; 9 8 6; 10 7 9; 11 9 10;
12 10 8; 13 3 11; 14 6 13; 15 8 14; 16 10 15; 17 11 12; 18 13 11; 19 14 13;
20 15 14;
DEFINE MATERIAL START
ISOTROPIC STEEL
E 29732.7
POISSON 0.3
DENSITY 0.000283
ALPHA 1.2e-005
DAMP 0.03
END DEFINE MATERIAL
MEMBER PROPERTY AMERICAN
2 5 13 14 TABLE ST W16X26
8 11 15 16 TABLE ST W16X26
1 3 4 6 17 18 TABLE ST W24X55
7 9 10 12 19 20 TABLE ST W24X55
CONSTANTS
MATERIAL STEEL ALL
SUPPORTS
1 4 12 FIXED
DEFINE PUSHOVER DATA
FRAME 2
FYE 36.000000 ALL
GNONL 1
DISP X 15 JOINT 10
LDSTEP 250
SPECTRUM PARAMETERS
DAMPING 5.0000
SC 1
SS 1
S1 1
SAVE LOADSTEP RESULT DISP 0.010000
END PUSHOVER DATA
LOAD 1 LOADTYPE Gravity
SELFWEIGHT Y -1
MEMBER LOAD
2 5 8 11 13 TO 16 UNI GY -.4
PERFORM PUSHOVER ANALYSIS
FINISH
Figure 1: Capacity Curve for a Structure in STAAD.Pro V8i
Figure 2: Deflected shape at specified displacement for a Structure in STAAD.Pro V8i
Figure 4: Beam Hinge results for a Structure in STAAD.Pro V8i
STAAD Results
P R O B L E M S T A T I S T I C S
NUMBER OF JOINTS/MEMBER+ELEMENTS/SUPPORTS = 15/ 20/ 3
SOLVER USED IS THE IN-CORE ADVANCED SOLVER
TOTAL PRIMARY LOAD CASES = 1, TOTAL DEGREES OF FREEDOM = 36
NUMBER OF MODES REQUESTED = 1
NUMBER OF EXISTING MASSES IN THE MODEL = 24
NUMBER OF MODES THAT WILL BE USED = 1
STAAD PLANE -- PAGE NO. 3
CALCULATED FREQUENCIES FOR LOAD CASE 2
MODE FREQUENCY(CYCLES/SEC) PERIOD(SEC)
1 1.292 0.77396
MASS PARTICIPATION FACTORS IN PERCENT
MODE X Y Z SUMM-X SUMM-Y SUMM-Z
1 79.94 0.00 0.00 79.944 0.000 0.000