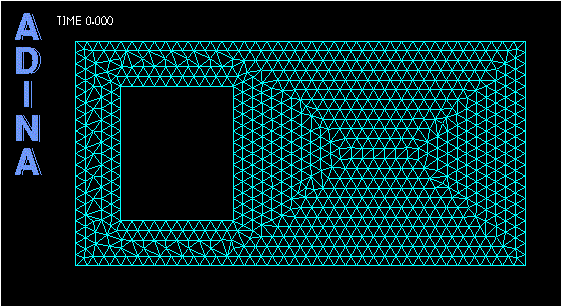
Steered Adaptive Meshing in ADINA — for FSI
In our previous Tech Brief, the use of the ADINA steered adaptive meshing (SAM) in a CFD solution is presented. Typically in a CFD analysis, the boundaries do not move and adaptive meshing is used to refine the mesh in certain regions of the model to improve the accuracy of the solution.
In a fluid-structure interaction (FSI) analysis however, the structural boundaries will move and distort the fluid mesh during the solution. If the boundary movement is significant, it may cause the mesh near the moving boundary to become invalid and the solution will fail. Hence, in an FSI analysis, adaptive meshing is often required to repair the mesh in order to achieve the solution, making it an even more challenging task. In this Brief, we will present the use of the ADINA steered adaptive meshing (SAM) for mesh repair during an FSI solution by working through an example.
Although SAM is applicable for general 2D and 3D models, we will use a simple 2D example where the mesh repair can be clearly observed, as shown in the animation on top. The schematic of the problem is shown in Figure 1.
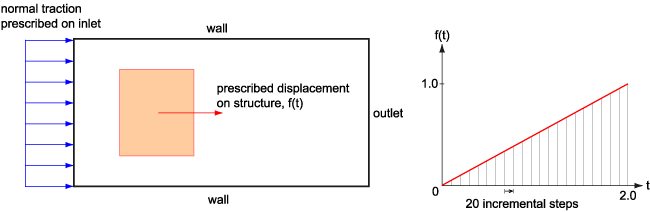
Figure 1 Schematic of the FSI problem
The purpose of this example is to highlight the steps required for setting up the SAM procedure for an ADINA FSI analysis. Prior to setting up SAM, the usual steps in setting up the basic FSI fluid and structural models are followed to obtain the batch input files that can be read directly into the ADINA User Interface (AUI). The batch files for the fluid and structural models are sam_f_0.in and sam_a_0.in respectively. Note that the use of the ADINA Modeler (ADINA-M) is required for SAM.
Procedure for setting up SAM in ADINA FSI
- Two batch files, easily, as usual, are constructed with the AUI (sam_f_0.in and sam_a_0.in) containing the FSI model for the fluid and structural parts, and are required for this example. Note that 20 incremental steps are prescribed for the analysis.
- We will first set up the fluid model for SAM. Start the AUI and select the ADINA CFD Program Module.
- Open the batch file via menu: File > Open Batch... Select sam_f_0.in and click Open.

- You should see the following fluid mesh with the loads and boundary conditions which defines the complete fluid model for a normal FSI analysis not using SAM.
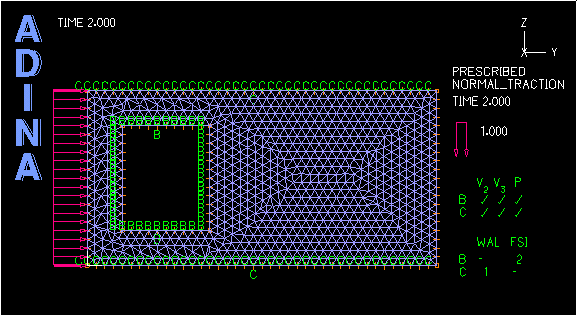
- We will now proceed to specify the necessary input for setting up SAM for the fluid model. Click on menu: Meshing > Steered Adaptive Mesh > Criterion... to define a criterion for the SAM procedure. In the dialog box, click on Add..., select Sphere Region type, specify the sphere radius and element size as shown and then click OK. Note that the center of the sphere (0,0,0) corresponds to the bottom left corner of the fluid mesh and 0.05 corresponds to the original mesh size of the model.
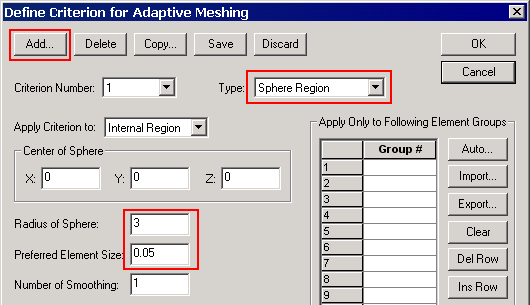
- Click on menu: Meshing > Steered Adaptive Mesh > Control... to specify the SAM settings for this analysis. In the dialog box, select Automatic mode, criterion 1 which was defined in the previous step and specify solution time of -1. Then click OK.
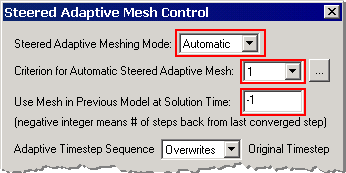
- This completes the SAM setup for the fluid model. We can now generate the data file for the fluid model. Click on menu: Solution > Data File/Run... Specify file name "sam_f_0" and make sure Run Solution is unchecked since this is going to be an FSI analysis using SAM. Click Save to generate the data file.
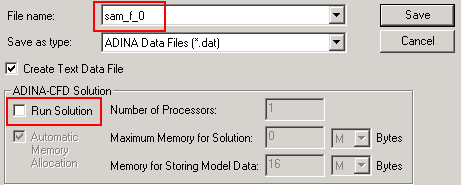
- A Log Window will appear which says that the following three files are created successfully.
Adaptive mesh file - sam_f_0.adp
Adaptive input file - sam_f_adp.in
ADINA-F data file - sam_f_0.dat
These files are necessary for the automatic SAM procedure. You can close the Log Window. - We will now proceed to set up the structural model for the FSI analysis using SAM. Click on menu: File > New. Click Yes when prompted whether you want to discard all changes and continue. Then, click on menu: File > Open Batch..., select sam_a_0.in and click Open. You should see the structural model as shown below.
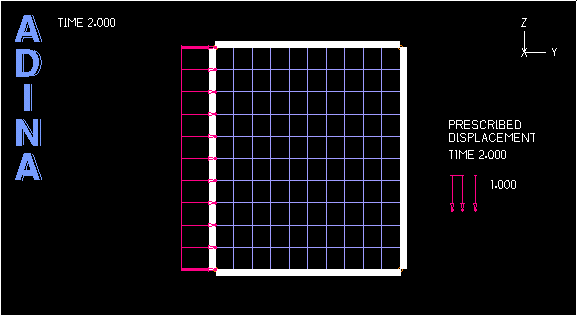
- Again, the structural model for a normal FSI analysis is fully defined by the batch file and we just need to add the settings to run the automatic SAM. Click on the Coupling Options button.

- In the SAM dialog box, select Automatic SAM mode, specify -1 for solution time and click OK. This is all that is required for setting up SAM in the structural model.
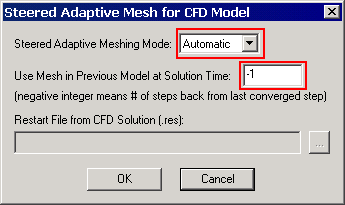
- To generate the data file for the structural model, click on menu: Solution > Data File/Run... Specify file name "sam_a_0", make sure Run Solution is unchecked and click Save.
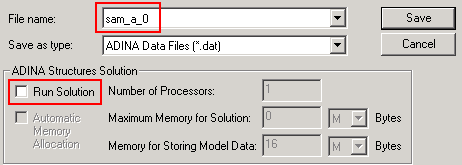
- In the Log Window, you should see the message that the following files required for the SAM run are successfully created. Go ahead and close the Log Window.
Adaptive mesh file - sam_a_0.adp
Adaptive input file - sam_a_adp.in
ADINA data file - sam_a_0.dat - We are now ready to launch the automatic SAM procedure for this FSI problem. Click on menu: Solution > Steered Adaptive... Then, click on Start which will open up the dialog box for specifying the options for the SAM run. Select the two data files "sam_a_0.dat" and "sam_f_0.dat" and specify the other parameters as shown below. Then, click Start to run the analysis.
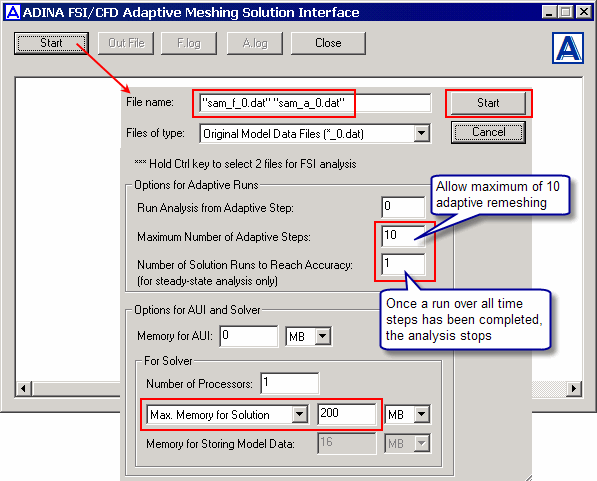
Here an Adaptive Step is defined as "remeshing". Hence a maximum of 10 remeshings are allowed. Also, Number of Solution Runs to Reach Accuracy equals 1 means that once the solution has been carried out over the complete time span, no additional step will be performed. If the parameter is greater than 1, additional steps will be performed for accuracy improvement based on a specified criterion.
- The messages in the SAM Solution interface track the progress of the SAM solution as highlighted below.
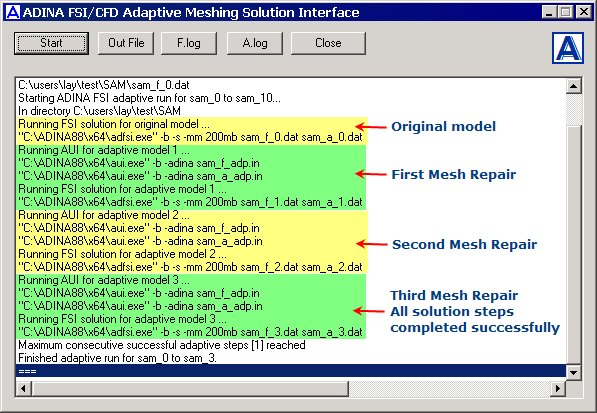
- To examine the results contained in the porthole files, we need to switch the module to Post-Processing.

- First, we open the porthole file for the original model. Click on menu: File > Open..., select "sam_f_0.por" and click Open.

- Next, we add the results for the three adaptive steps. Click on menu: File > Open Porthole..., select "sam_f_3.por", "sam_f_2.por", "sam_f_1.por", toggle on Add to Current Database and click Open. You can then proceed to examine the results which should show the three mesh repairs performed during the adaptive solution as illustrated in the animation at the top.
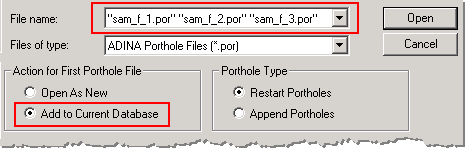
The following figure shows what has happened in the complete incremental solution (see also Figure 1).
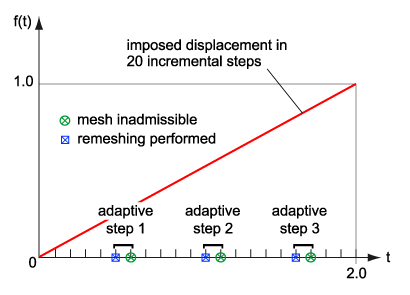
Figure 2 Solution process
Changing Adaptive Criterion during SAM
In the above example, the final solution was reached in 20 steps after three adaptive remeshings using the same original criterion. Sometimes, the original adaptive criterion may not achieve a converged solution all the way to the final time step and it is necessary to change the criterion and restart the analysis from a certain adaptive step. A change in the criterion is also quite easily prescribed and is illustrated in the steps below.
- Follow all the steps in the above example except for step 5. Instead of defining the adaptive criterion of type Sphere Region, let us define the criterion based on Element Quality with the default parameters.
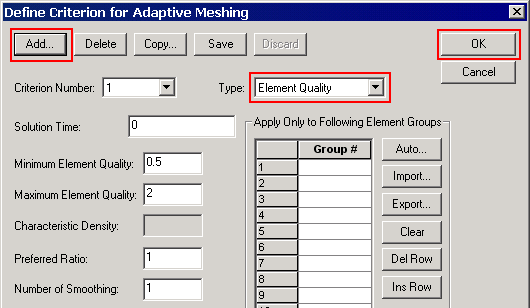
- After generating the data file like in step 7 above, we can proceed with the SAM Solution. Note that there is no change to the structural model setup. Start SAM as in step 14 above. The SAM Solution interface will show the following messages where we observe that the fourth adaptive meshing fails. This is because the analysis using the adaptive mesh 3 fails to produce a converged solution for even a single step. Hence, the SAM procedure cannot continue further.
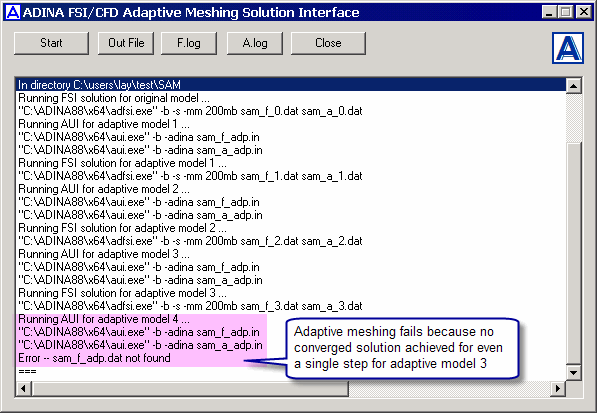
- We follow steps 16 to 18 above to open the porthole files and examine the adaptive meshes. Looking at the first adaptive mesh (at solution time 0.6), we see that the criterion is rather ineffective in repairing the mesh.
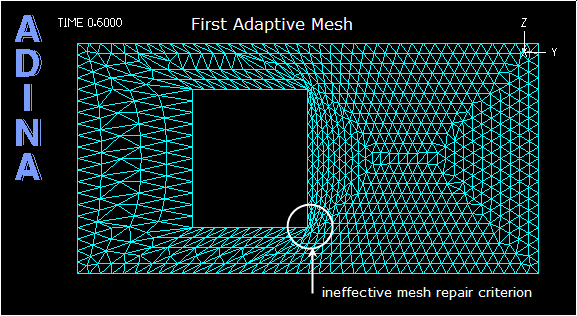
- We will modify the adaptive mesh criterion by editing the file "sam_f_adp.in" that was created automatically by the AUI during data file generation (see step 8 above). Use a text editor, e.g., Notepad, to open the file and modify the minimum and maximum values for element quality. Since the default values are too loose for this problem, we will set both values to 1.0.
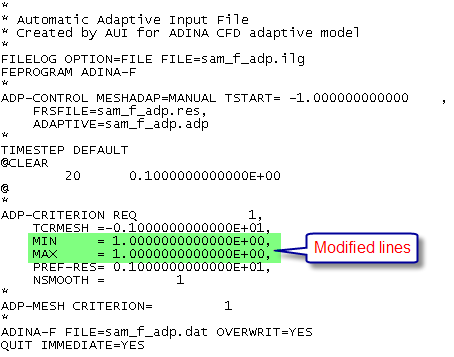
- Although the SAM procedure was able to achieve converged solutions in the second adaptive step, we will restart our solution from the first adaptive step since the first adaptive mesh already does not look good. In general, the user can choose to restart the procedure from any adaptive step that has at least one converged solution. Start SAM again as in step 14 above. Note that we still select the data files "sam_a_0.dat" and "sam_f_0.dat" but we specify to start from adaptive step 1.
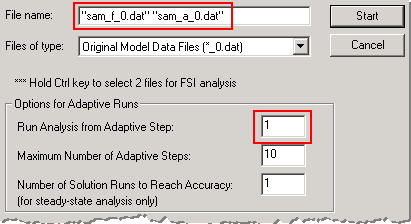
- With the modified criterion, the analysis completed successfully with three adaptive remeshings.
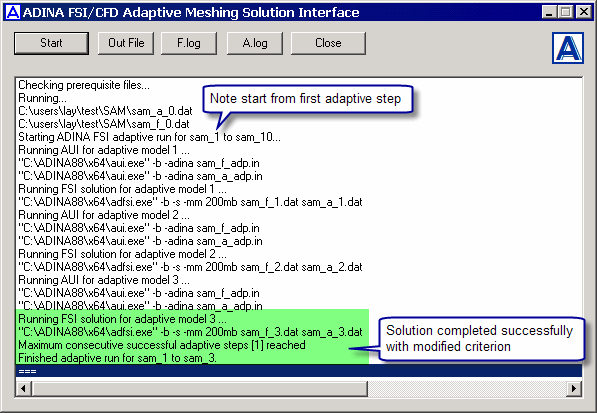
Remarks
In summary, the SAM procedure is powerful and rather flexible. The procedure also offers various other options that are not discussed in this presentation. In particular, it is possible to perform the adaptive meshing interactively within the AUI to evaluate the new meshes created by different criteria and then decide which criterion to use. This approach of performing FSI simulations will undoubtedly enable ADINA users to solve many difficult FSI problems more easily and in particular solve many new challenging problems that could heretofore not be tackled.
Keywords:
Meshing, adaptive meshing, mesh repair, CFD, FSI, free-form meshing, error control, 2D and 3D solutions