Hook Up Tool (Enhanced Tool):
- The Hook Up tool has been re-written to improve upon the existing tool and add more capability, this tool offers automated options on hook up routing and increases stability of the tool. This tool is now available within the ribbon interface rather than as a stand-alone dialog box. Fittings generated during hook-up process are based on user defined auto-fitting preference settings.
- Hook Up options:
- Calculated:
- User will be presented with calculated routes that are based on the optimized paths. There may be multiple options to choose from that are shown in single line dynamics, user can toggle through these options and accept preferable solution. These solutions include both side connections to the nearest face or top/bottom duct connections based on orientation.
- User defined settings like angle, flex length and item type will be incorporated in the calculated solution paths
- Free form:
- Similar to previous functionality, user can dynamically manipulate the hook up route by cursor movement that is reflected on screen with single line path representation.
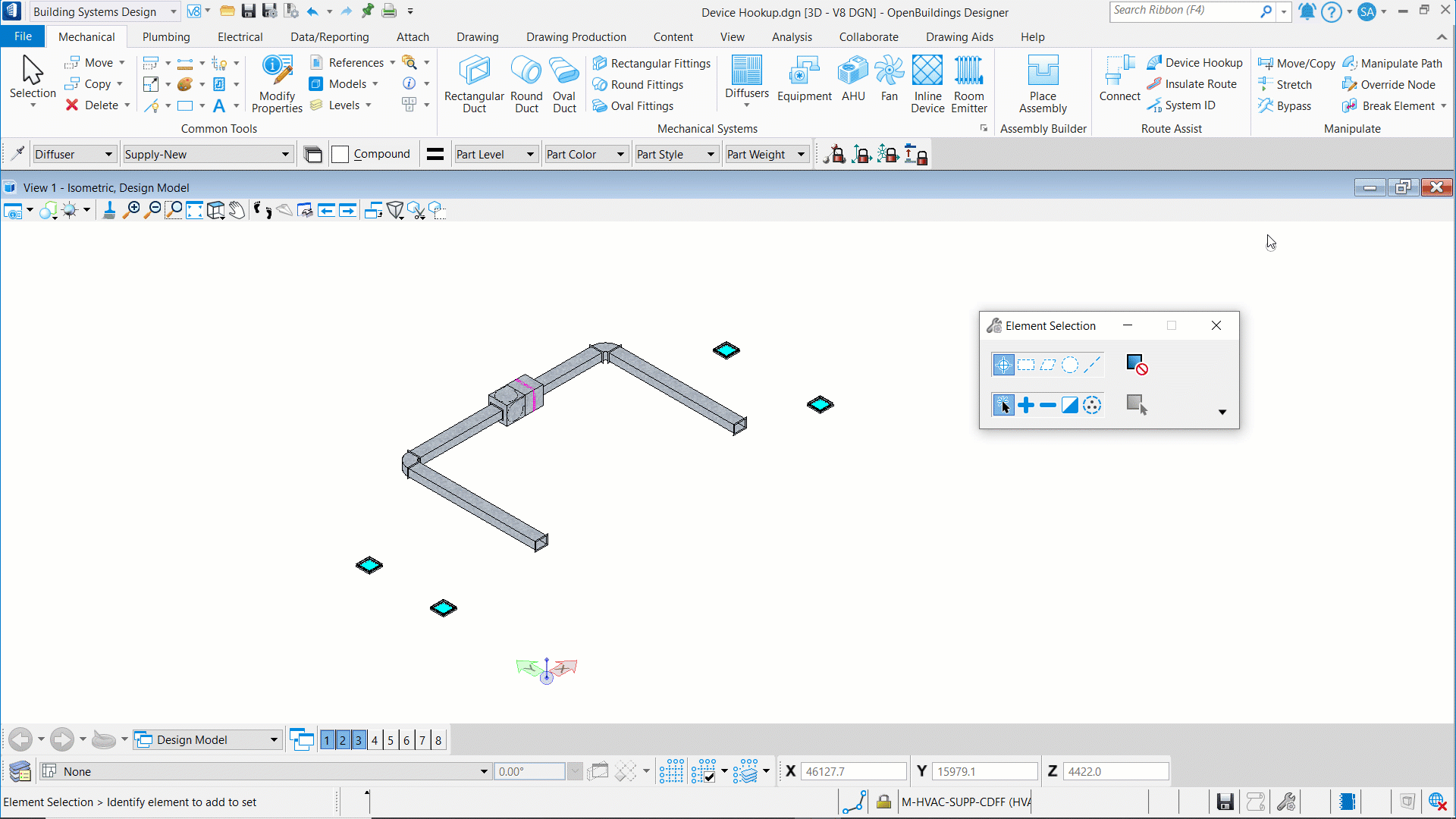
- Hook Up settings:
- Selection set: Multiple terminal devices can be selected so that hook up takes care of multiple connections, this capability replaces the need to use Fence in the previous tool.
- Group: This functionality enhances the use of selection sets to let the user visually see and manipulate the single line path to adjust how a group of terminal devices are connected to the piping or duct system. This allows the user to adjust how and where branch take-offs and subsequent final connections are made, note that this capability can only achieve results with 90°connection angles.
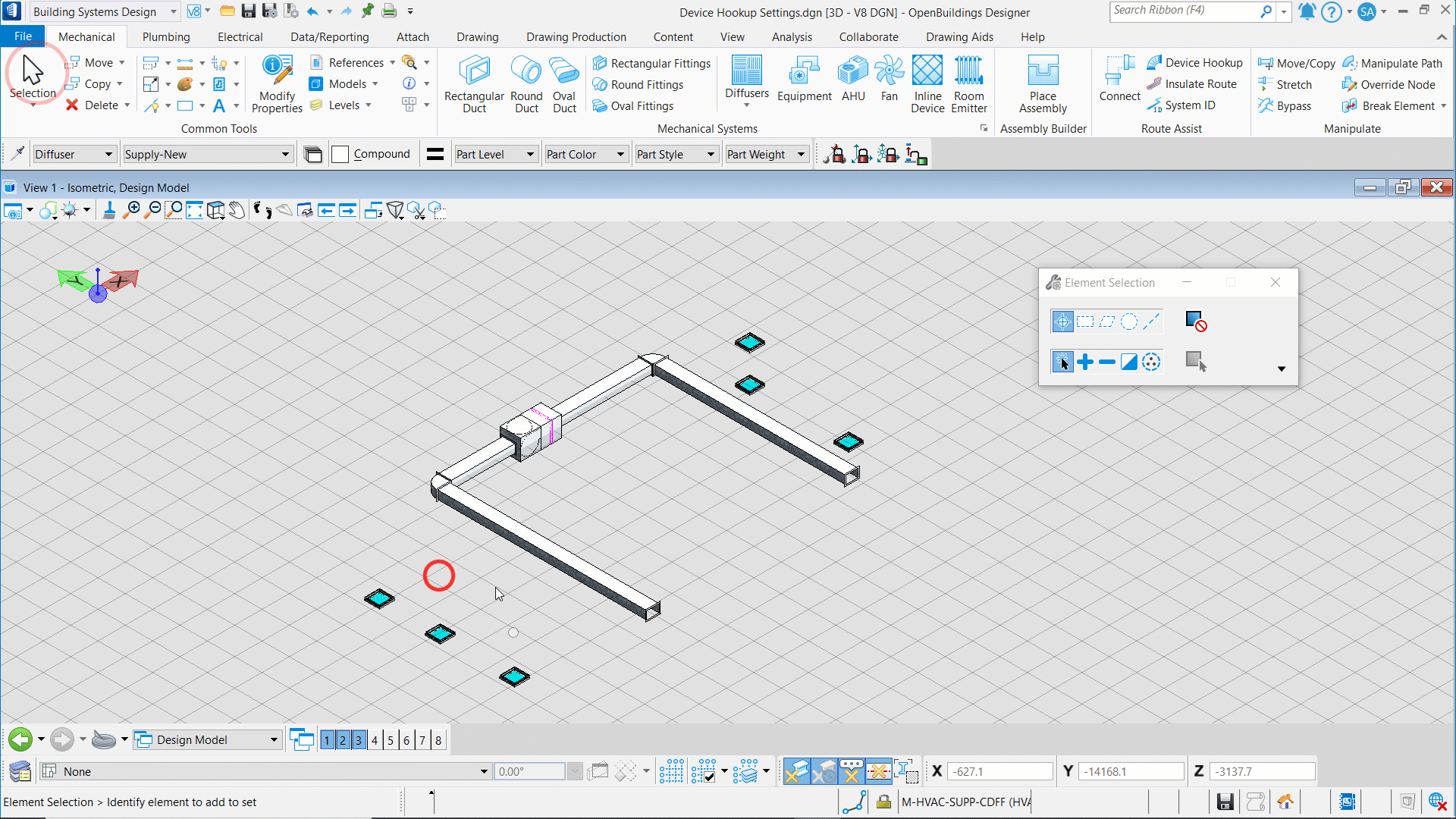
Content Creator
- Content Creator allows users to import a static cell and attach mechanical connection ports along with DG data from a similar existing component within OBD Data Group. During the process of creation user should be able to save the content to a standard or user defined location and reuse created components.
- Cell can be user created using MicroStation tools or by importing and converting 3rd party content into a cell
- Discipline specific, intelligent connections points can be accurately placed on any cell to allow duct and piping connections. These points contain user defined information for size, shape and discipline.
- Placement points can be located anywhere on the cell at user defined locations and are shown in the placement preview which allows selection of any of these points for placement.
- Modification allows the user to edit both placement point as well as any of the content connector attributes
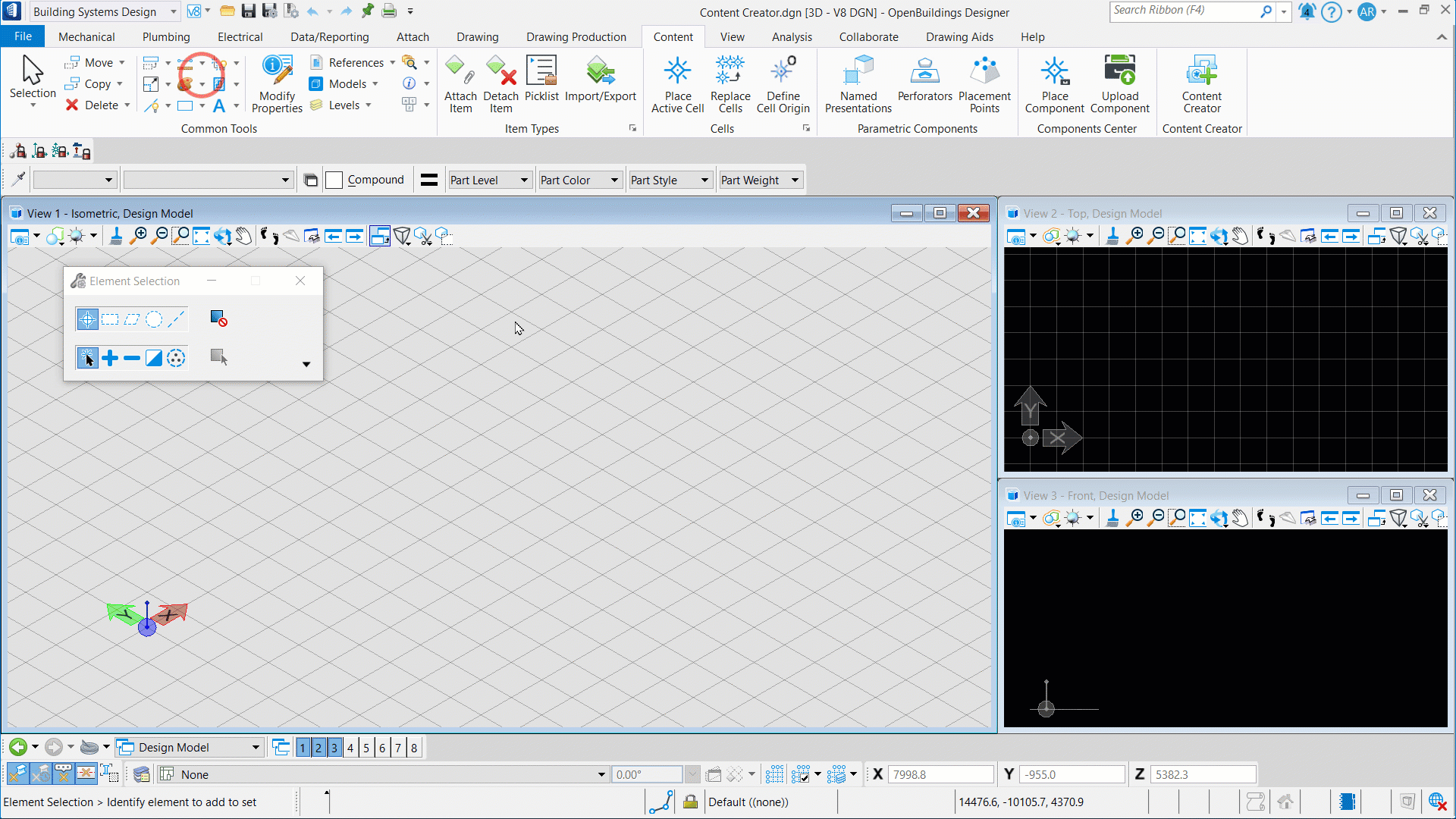
Exchange Component
- The exchange options allow the user to replace a single component with another component type. User will manually connect the fitting to existing system. The tool will replace the selected component. The connected end will be aligned only if size option in the ribbon is ON.
Mechanical Copy
- Right click on a component now offers the user the option of Move / Copy component. This new option extends the functionality of this tool by creating copies instead of just a move. Once a system or assembly of duct/pipe is setup, the tools Copy component option will allow us to quickly copy a connected system based on a single component.
- Mechanical Copy options:
- Number of copies option creates multiple copies spaced at a defined distance set by user.
- Copy along linear route re-heals the network interrupted by the insertion of new fittings
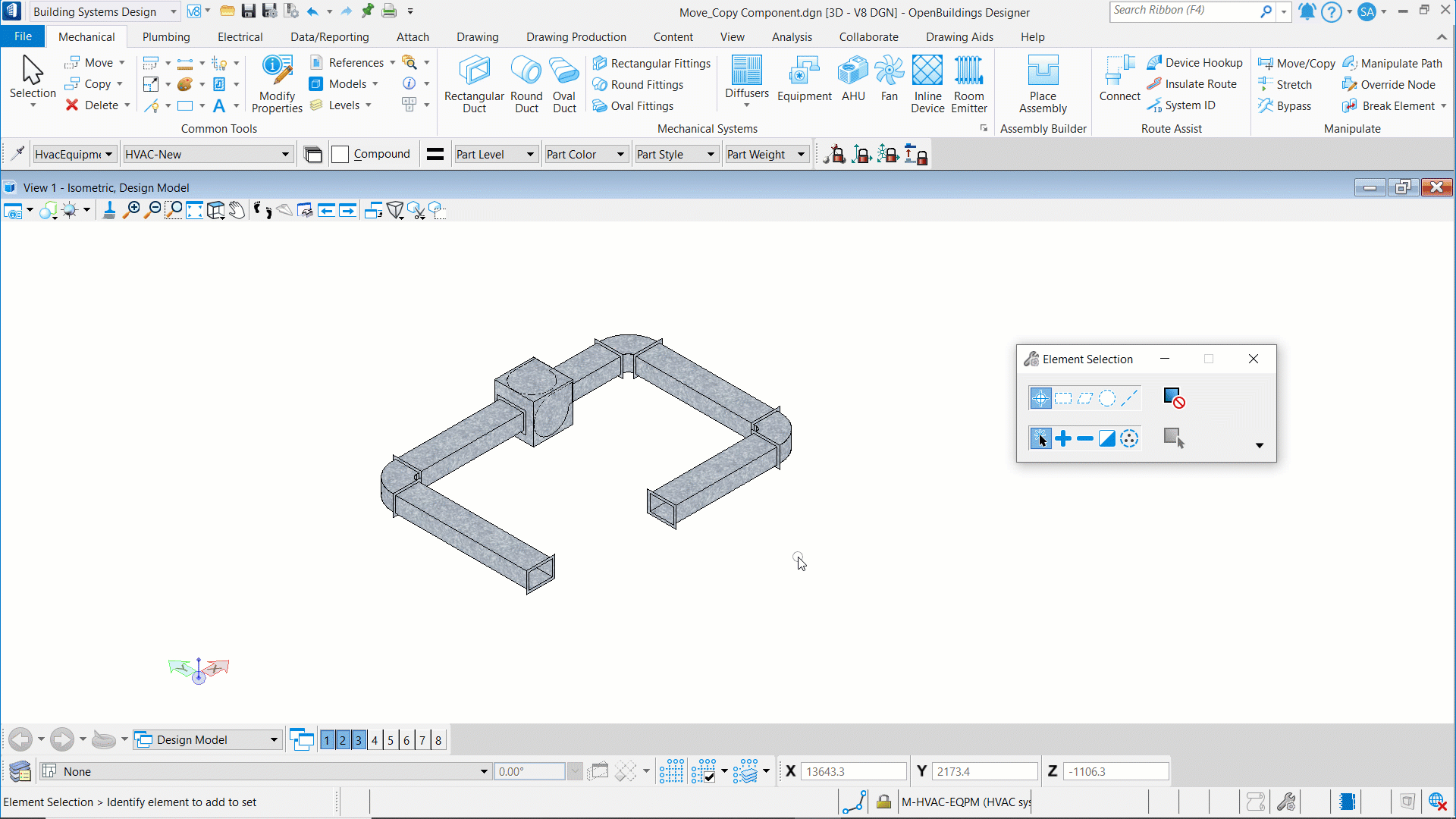
Apply Part for Mechanical Discipline
- Added option for Apply Part has been added to Rt. Click options in mechanical disciplines, this allows user to edit Part definition of a component(s)
HVAC Auto-Fitting Preferences
- Cross Fitting added as selectable option for automated placement
- For consistency and user convenience the Auto Endcap options has been relocated from the user preferences dialog to the Autofitting preference dialog for both HVAC and Piping.
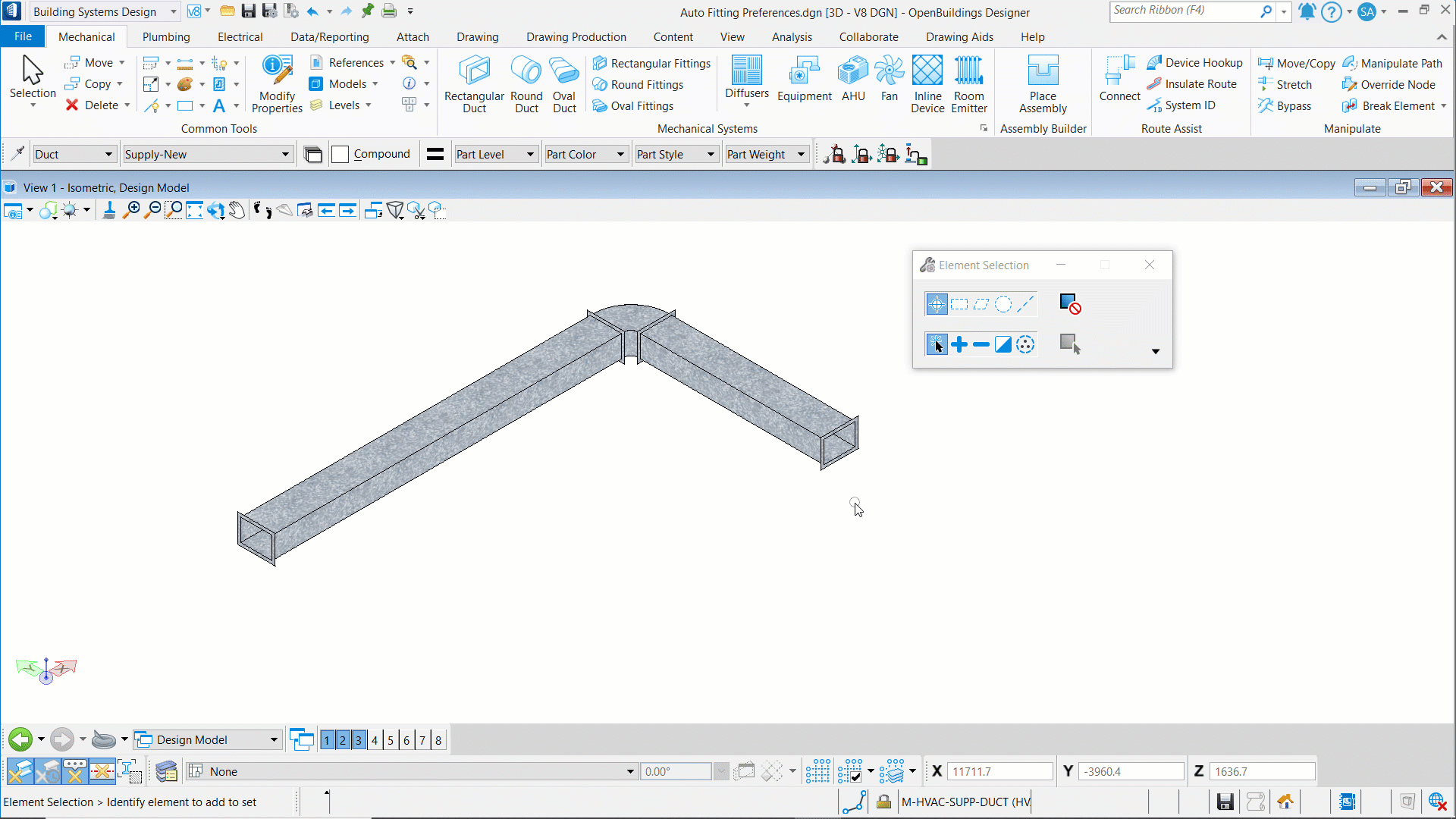
Assembly Builder
- User now has option to select and modify placement point for assembly
- Added base offset capability for accurate placement
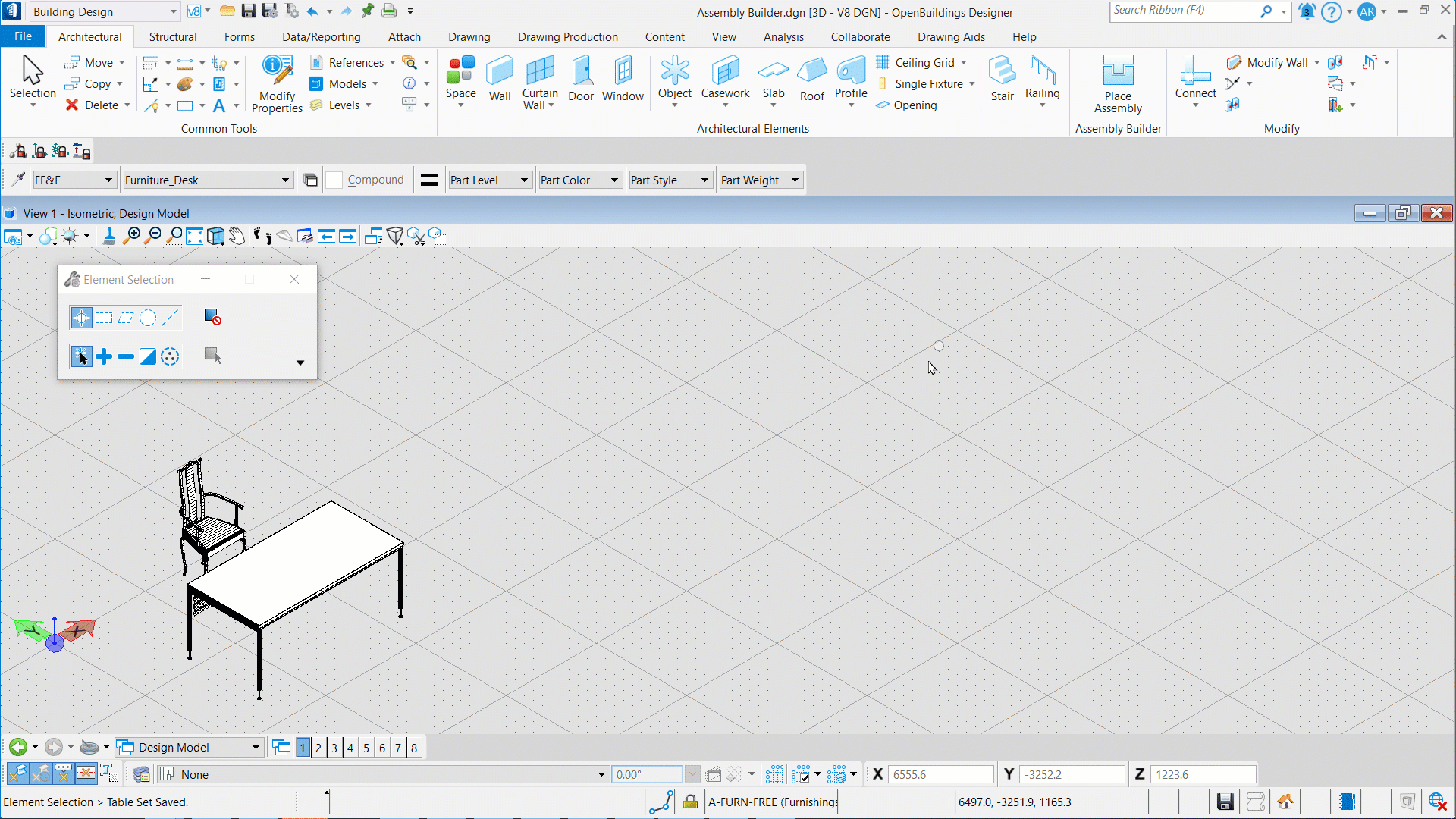
BMECH Rebuild
- We have included this option in File>Backstage to allow user to instantiate BMECH Rebuild command which upgrades the element symbology attributes of elements placed in previous product versions.
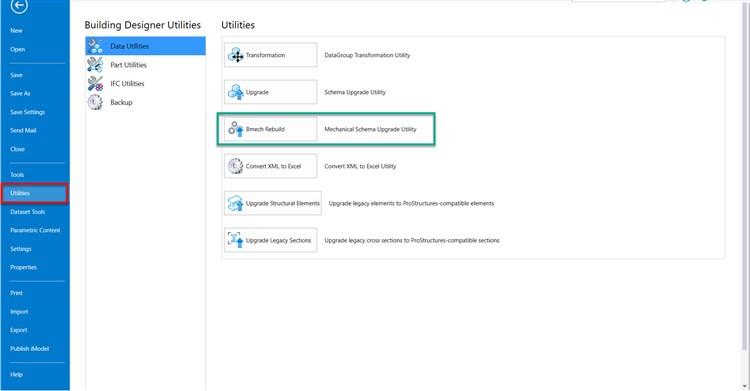